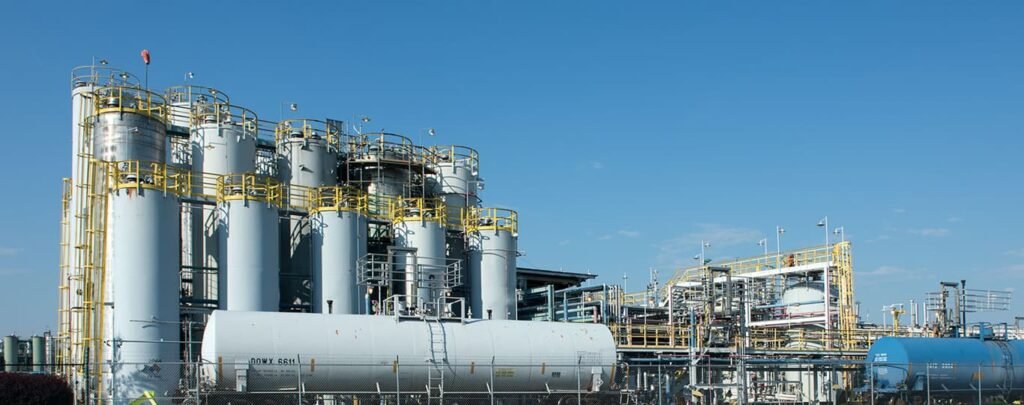
Chemistry factory greatly improved the lifetime of sealing ring and saved labor costs by using modified rubber material.
Country: South Africa
Industry: Chemical
Technology: Material Modification
John Smith, a customer from South Africa, currently operating a chemical plant covering an area of 25,000 square meters. It mainly produces chemical reagents and other fine chemical products, and has gained a firm foothold in the local area with years of industry experience.
However, this company has always had a problem. Due to the high-intensity operation of the equipment and the special use environment, the O-type rubber sealing ring of the equipment’s supporting parts is very easy to wear out. On average, it needs to be replaced every 3 months. At the same time, the machine will stop running, special personnel needs to be arranged to replace the new sealing ring, which is very time-consuming and labor-intensive.
In order to solve this problem, John Smith consulted many parts manufacturers and asked if they could customize a long-life rubber seal ring, hoping to reach more than 3 years. As one of the candidates, our rubber injection molding companies have rich experience and advanced equipment. After understanding the customer’s special needs, Mr. Li asked the customer to send a sample of the sealing ring in use, and through professional testing and analysis, the original material was improved in multiple dimensions, and the rubber sealing ring was finally produced. As a result, it not only has a good anti-stretch effect, but also has high temperature and pressure resistance, good anti-aging and corrosion resistance.
After the customer has used our customized sealing ring, it has not been replaced in the past 3 years. John Smith is pleased to comment “This is the most professional rubber parts manufacturer I have worked with. Thank you very much. My production efficiency has been greatly improved! “