Molding processes play a key role in modern manufacturing. Molded products can be found everywhere in our lives, from consumer electronics to everyday containers and automotive parts. Blow molding and injection molding are two widely used manufacturing processes. Each process with its unique characteristics, advantages, and applications. Let’s compare the differences and similarities between blow molding and injection molding. By the end of this comparison, you’ll have a clear understanding of when and why to choose one over the other, depending on the specific manufacturing needs.
What is Blow Molding?
Blow molding is a highly versatile manufacturing process that involves the creation of hollow plastic parts or containers by inflating a molten thermoplastic material into a mold cavity. This process relies on the application of air pressure to shape the material within the mold, resulting in a wide range of products, from plastic bottles to automotive components.
Extrusion Blow Molding:
In extrusion blow molding, a continuous parison (a tube-like plastic) is extruded vertically or horizontally from an extruder. The parison is then clamped into a mold, and air is blown into it to inflate and conform to the mold’s shape. This method is commonly used for producing items like plastic bottles and containers.
Injection Blow Molding:
Injection blow molding combines aspects of both injection molding and blow molding. A preform is injection-molded, which is a small, solid piece of plastic with the desired final shape. This preform is then reheated and placed in a blow mold, where it is inflated to take on the final product shape. Injection blow molding is often used for small, precise parts.
Stretch Blow Molding:
Stretch blow molding is primarily used for producing PET (Polyethylene terephthalate) bottles, such as those used for beverages. It involves stretching a preform while simultaneously blowing it into the final bottle shape. This process results in lightweight, high-strength bottles with excellent clarity.
Advantages of Blow Molding:
- Blow molding is well-suited for large, hollow products like bottles and containers.
- Blow molding typically involves lower initial tooling costs compared to injection molding. The molds used in blow molding are simpler, making them more affordable to manufacture.
- Blow molding is highly material-efficient because it creates hollow shapes.
Disadvantages of Blow Molding
- Compared to injection molding, blow molding is primarily suited for creating hollow plastic products. That manufacturing process limited its versatility.
- In certain types of blow molding, such as stretch blow molding, the cycle times are longer.
- The process can not provide the same level of precision and detail as injection molding due to the simple design and tools.
Application of Blow Molding
Blow molding is a cost-effective manufacturing process widely used for various industries and products.
Bottles and Containers: Blow molding is widely used to manufacture plastic bottles and containers for beverages, cosmetics, cleaning products, and more.
Automotive Components: Many automotive parts, such as air ducts, fuel tanks, and interior trim components, are produced using blow molding due to their ability to create complex hollow shapes.
Consumer Goods: Products like toys, sports equipment, and storage containers often employ blow molding for their lightweight and durable characteristics.
Medical Equipment: Blow molding is utilized in the production of medical devices and equipment, including surgical trays, oxygen masks, and IV bags.
Industrial Products: Industrial applications include the production of drums, barrels, industrial tanks, and large containers for chemicals and other fluids.
Packaging Materials: Blow molding is used to create packaging materials like plastic film, bags, and industrial liners.
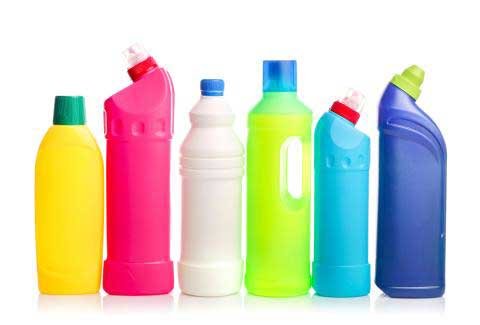
What is Injection Molding?
Injection molding stands as one of the most widely employed manufacturing processes, renowned for its precision and versatility. It involves the creation of three-dimensional plastic parts or products by injecting molten thermoplastic materials into a mold cavity under high pressure. Upon cooling and solidification, the material takes on the shape of the mold, producing a vast range of items found in nearly every industry.
Advantages of Injection Molding
- Injection molding allows for complex geometries with tight tolerances.
- Injection molding is efficient for high-volume production. Once the injection mold is ready, the manufacturing process is very fast.
- Injection molding is compatible with a wide range of materials. Today, there are over 25,000 engineered materials that are compatible with injection molding, including thermoplastics, thermosets, resins, and silicones.
Disadvantages of Injection Molding
- The start-up costs are high. Since custom tooling must be created for each injection molded part, initial start-up costs are high and this isn’t economical for low-volume production runs.
- The initial lead times are long. Injection molding has a longer lead time. It often takes 5-7 weeks to manufacture tooling.
- Design changes are expensive. Sometimes, if you make a design change for an injection mold, you will likely need to create a new mold from scratch.
Application of Injection Molding
Injection molding is a highly versatile manufacturing process. It excels in producing precise and intricate plastic components used in consumer electronics, automotive parts, medical devices, and more.
Consumer Electronics: Injection molding is extensively used to produce components for consumer electronic devices such as smartphone cases, computer housings, and keyboard keys.
Automotive Parts: Many automotive components, including dashboard panels, interior trim, exterior body parts, and engine components, are manufactured using injection molding.
Medical Devices: Injection molding is crucial for producing medical equipment and devices like syringes, IV connectors, and surgical instruments due to its precision and sterile production capabilities.
Industrial Equipment: Injection molding is applied to create various industrial parts, including gears, valves, and machine components.
Electrical Components: Components for electrical systems, such as connectors, switches, and wire harnesses, are manufactured using this process.
Differences Between Blow Molding and Injection Molding
Understanding the blow molding and injection molding comparison can only be effective by understanding their differences. Below are a few differences between blow molding and injection molding and how to tailor them to your project.
Different Molding Processes
Blow Molding Process
Blow molding starts with a heated plastic tube, which is inflated with air until it forms a hot plastic “balloon” called a parison. A mold then closes around this parison, capturing the plastic while air continues to fill it, shaping it precisely into the desired part.

Injection Molding Process
Injection molding begins with thermoplastic pellets that are melted and injected into a mold cavity under high pressure. The mold, containing the negative shape of the desired part, closes to form the product. After cooling and solidification, the mold opens, and the finished part is ejected.
The key difference is the usage of air, inflated in blow molding or injected into a mold in injection molding.
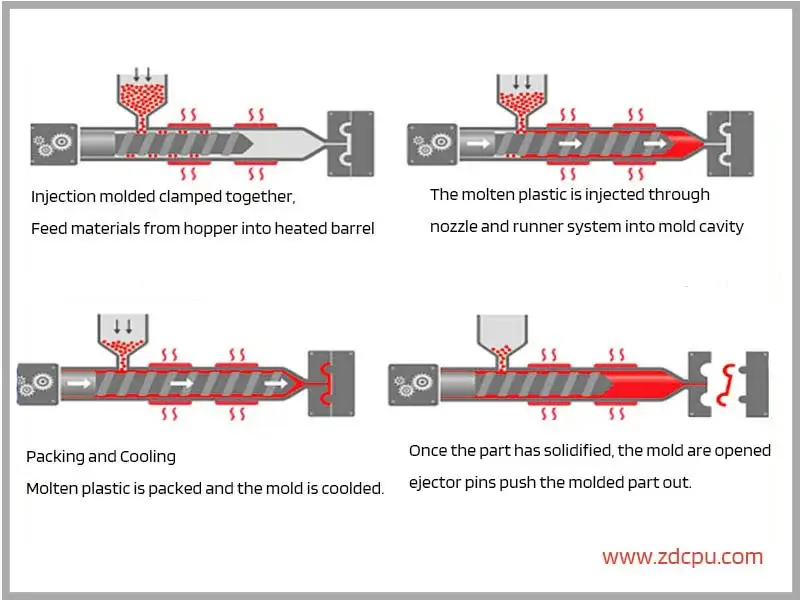
Different Molding Materials
Common materials used in both blow molding and injection molding include PE, PP, and PC. They are thermoplastics, meaning they can be melted and molded repeatedly, making them suitable for both blow molding and injection molding.
While the materials listed above are commonly used in both processes, each process may have unique materials or variations tailored to its specific requirements:
Blow Molding:
For blow molding, materials like PET (Polyethylene terephthalate) are unique. PET is well-suited for stretch blow molding, producing lightweight, high-strength bottles and containers. It’s less commonly used in injection molding.
Injection Molding:
Injection molding is suitable for thermoplastics, engineering plastics, elastomers, and rubber. For example, ABS (Acrylonitrile Butadiene Styrene) is an excellent thermoplastic material known for its toughness. Nylon is known for its strength, durability, and resistance to abrasion which are frequently employed in injection molding.
Different Products Manufactured by Each Process
Blow Molding:
Primarily excels in producing hollow, container-like products, especially bottles, and containers for liquids and goods.
Injection Molding:
It can produce versatility and high-degree precision solid components.
Different Molding Cost
The costs of these two molding methods are also different. We can compare them in terms of mold cost, material cost(material efficiency), and time cost (cycle times).
Cost Aspect | Blow Molding | Injection Molding |
---|---|---|
Tooling Costs | Lower initial tooling costs | Higher initial tooling costs |
Material Cost | Efficient due to hollow shapes | Potential material waste |
Time Cost | Longer cycle times | Shorter cycle times |